Skins
Generally, tribes in Wisconsin made soft-soled moccasins due to the terrain. Though Native Americans used a lot of different skins - such as deer, moose, bear, caribou, elk, rabbit, and beaver - buckskin was the most desirable for moccasins; it is warm, durable, and does not tear easily. One large buckskin could make around nine moccasins, and is usually dehaired. In winter, the hair was left and turned inside out for warmth, and some moccasins were made with high tops to cover the calf of the leg.
Some moccasins can be made from a single piece of skin, but some can be made of multiple pieces, though only what is needed and depending on which tribe is making them. Some moccasins have an added vamp (the front part of the shoe) over the toes and an individual piece for a broad cuff or flap.
The preparation process for the skins was long, and there were various ways to do the process to achieve different finishes. These finishes varied in quality, color, and texture. The color is determined by what wood is used in the smoking process, the time it took to smoke the skin, and the type of skin.
Wearing buckskin everyday had its share of problems. When wet, it would stiffen and become clammy and cold, leading to the need of reprocessing; it would also wear out faster than a modern shoe. One man needed five or six pairs of moccasins if they were going on a journey on foot. Women would have to prepare those moccasins in advance to make sure everyone had enough, and men would have to hunt the deer, preferably when the skins were at their best, which was Fall when their coats were at their thickest. Without the preparation, Native Americans would have to go without proper protection, leading to problems when winter came.
Decorating
When it came to decorating the moccasins, porcupine quills were used as they were the easy to acquire. They could be dyed to many different colors, and once dyed they would be prepared for quillwork. First, the quills were softened by soaking them in water. Second, they were flattened by holding one end of a quill between the teeth and then flattened with the crafter’s thumbnail. Quills then would be sewn on with one of many styles of stitches to form patterns.
Quillwork was -and is- a highly skilled and imaginative style, some quillers perfecting their own style, a skill still used today that is intricate and highly sought-after in design. Some quills would be braided in complex ways, or folded to produce different visual effects and textures.
The dyes used in quills came from plants and minerals. Some examples include the inner bark of red-osier dogwood, butternut or white walnut tree bark or root, the inner bark of sumac, and rotten maple wood. Today, people use Rit dye.
Beads were first made of bones or shells, but were not as used in embroidery in prehistoric Wisconsin. Glass beads were introduced by Europeans and generally replaced quillwork, though some crafters kept working with quills.
When Europeans came, new materials were introduced, such as stroud, woollen, and cotton cloth, though animal skin was still used for moccasins.
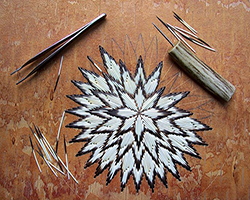
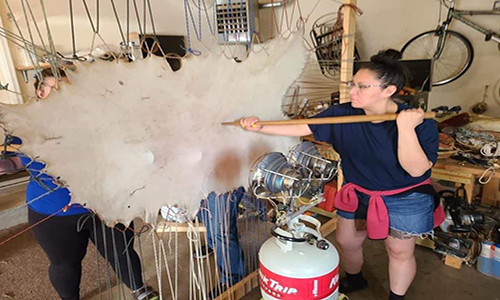